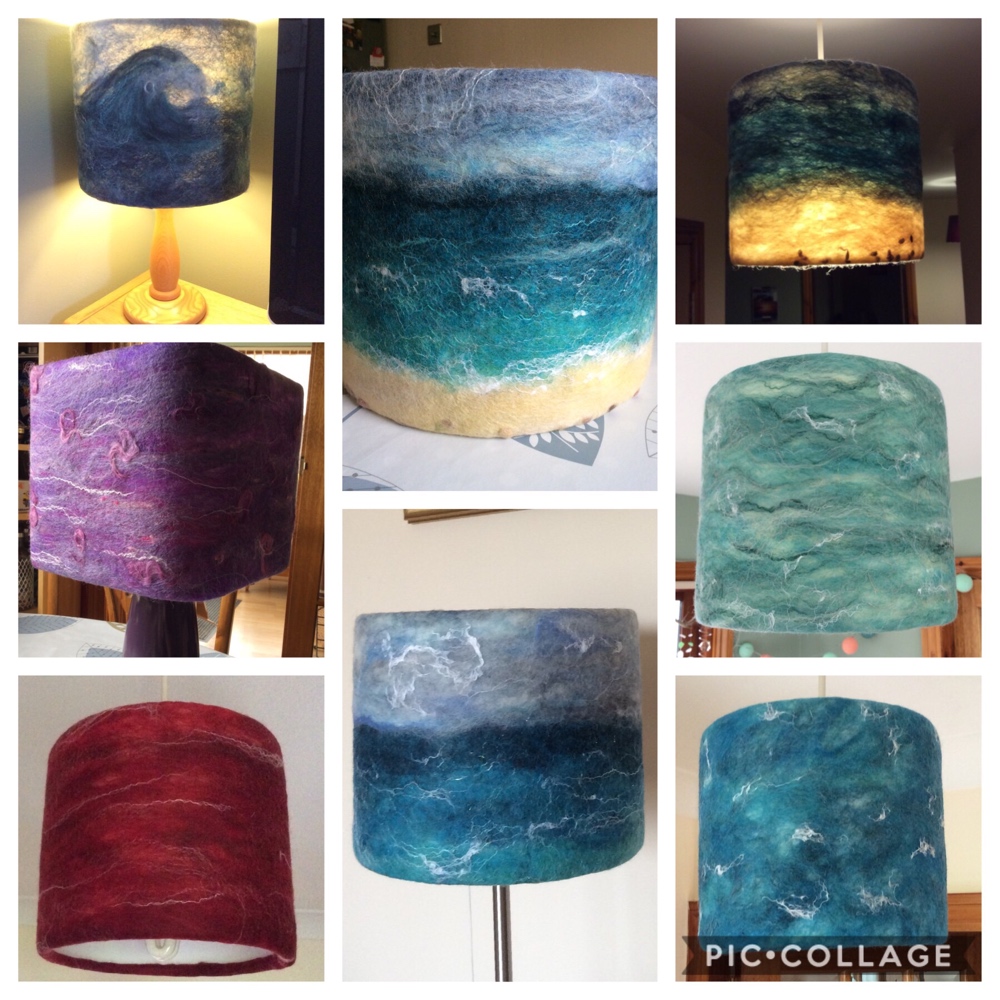
There are numerous examples of lampshades I have made throughout my blog, but I thought now I’ve done a series of posts about how to make them it would be a good idea to add a Lampshade page.
A selection of lampshades are now for sale at the Alchemist Gallery in Dingwall, in the Highlands of Scotland. If you have bought one of the lampshades I hope you love it. My home is filled with them and given lampshades spend most of the day unlit, it’s nice to have a piece of art on display. If you have any queries about your lampshade then please read the details below and if you don’t find the answer please do feel free to message me.
On my Instagram page I have a Hyper-lapse video of me making a shade.

The lampshade kits I use have the following details:
Specifications
Your lampshade can be used on European and the UK (includes adaptor ring), so if your lamp is from IKEA, for example, then you just remove the adaptor ring).
Lampholder Types
B22 Bayonet Cap Lampholders (UK) Adaptor Fitted
E14 Edison Screw Lampholders (EU) Adaptor Fitted
E27 Edison Screw Lampholders (EU) Adaptor Removed
E26 Edison Screw Lampholders (US) Adaptor Removed
Lampshade Assembled Size
The ones I mostly offer are:
20cm Diameter x 18cm High
25cm Diameter x 21cm High
(Occasionally I have other size kits that I can use to make larger shades. Ordering small amounts of the kits is expensive for me, so doing bespoke orders for sizes I don’t have in stock is cost prohibitive. However, if you ask at the gallery they can get in touch and I will see if I have the kit size in stock to make one.)
Lining Colour
White.
Bulb Advice
The kit manufacturers recommend the use of low energy bulbs with your lampshades. They use less energy and are cool to the touch, avoiding the problem of scorching shades and ceilings.
Testing
The lampshade lining and wires have been tested by the manufacturer and passed the glow wire test carried out by the Lighting Association. Wool is naturally fire retardant, which is why it is used for fire blankets.
Visibility
When lit the landscape patterns may be less clear than when they are unlit. They will however show the textures and varying thicknesses in the fibres, that creates its own features.

The fibres I use are:
As far as possible I try to use wool from local/British sheep, rather than merino wool which is most often imported from Australia, South Africa and New Zealand.
- UK Shetland wool pre-felt base (I hand pick out any larger pieces of vegetable matter)
- The needle felted sheep are all made using wool from a friend’s sheep. They live on the hills not far from Loch Ness on Achpopuli Farm. The sheep’s name is Roxy and she is a BFL/Shetland cross.
- Some contain North Ronaldsay wool, that I bought in the Orkney Isles and dyed myself. These sheep are famous for eating seaweed and living along the coast of North Ronaldsay (an Orkney Isle). This breed has some white and black thicker curly hairs that I have removed a lot by hand, but some will have slipped through or been left to add a different texture.
- Some include wool from Corriedale cross sheep and other sheep breeds from a lady in Aberdeenshire who has her own sheep and sources fleeces from other locals.
- I have also dyed some merino, Corriedale and other wool fibres that are included in the lampshades
- The silks are often silk waste, left over from the manufacture of silk threads (throwster silk waste) and silk fabrics (sari silk waste).
- On the seascapes I often use some dyed flax fibre (the fibre used to make linen). I also use silk/flax waste mix for waves and sometimes silk/viscose waste. The pebbles are wool nepps.
- The angelina (sparkle) fibre is obviously manufactured rather than being natural, but sometimes it’s nice to do a lampshade that has a hint of sparkle!
- I have recently acquired a different Shetland cross fleece from a local lady that I am starting to wash and process.
Merino felts much quicker and with a lot less effort than the local breeds or locally sourced wool that I have bought, so they take more elbow grease but create much nicer textured finishes. However, I have done some purely in merino like the set of 4 shown below. There are some others blended with silks and flax that can be see in the lampshade slideshow on the Portfolio page as well. If you see a style you’d like me to replicate then get in touch through the contact form.

Other things you may like to know:
- I use olive oil soap during the felting process.
- I do not use any sort of adapted sander or felting machine to do the felting, these are all felted using a lot of elbow grease!
- There’s a lot of work that goes into each lampshade. Not including the time spent cleaning fleeces, dyeing and blending fibres, they take a few days to make. There’s cutting the pre-felt, laying out the design, wet felting the shades, adding needle felted detail where applicable and then trimming and constructing the lampshades, then creating a label and wrapping in cellophane (100% biodegradable).
- For the land and seascape shades I felt them enough where they are going to stay constructed but the individual fibres can still be seen in places, as this adds some texture to the cloudy skies, seas and land. They are sufficiently felted to clean them with a low tack lint roller though, but I don’t find I need to do that more than twice a year.
- The felting process does move fibres around and using different fibres comes with different shrinkage rates, so it is not always possible to have a neat join of the horizon at the back of the shade. As far as possible I will try to ensure they are level at the join.
[…] Lampshades […]
LikeLike
[…] Lampshades […]
LikeLike
These are beautiful 👌❤️
LikeLiked by 1 person
[…] Lampshades […]
LikeLike
[…] Lampshades […]
LikeLike
[…] Lampshades […]
LikeLike
[…] Lampshades […]
LikeLike
[…] Lampshades […]
LikeLike
[…] Lampshades […]
LikeLike
[…] Lampshades […]
LikeLike